Chemical etching has proven to be an increasingly popular method of manufacture as the trend for smaller, more delicate and complex devices has grown massively in recent years. ‘Micro Manufacturing’ as it’s known is only possible thanks to processes like chemical, laser or microforming that allow for such intricate and accurate metal shaping. As the demand rises for micro metal parts that contain zero flaws along with being structurally sound enough to function accurately in whatever instrument they end up in, manufacturing needs to innovate in order to keep up. This is what chemical etching has been able to achieve and on an industrial scale.
Uses
To begin with, chemical etching is a subtractive method of cutting and etching metals that is widely used across many varying industries. Speaker grilles, filters, fuel cell plates, encoder discs and many more products are all created by using the chemical etching process. The reason that these precise products are made using chemical etching is that they all require absolute precision, for instance there are many surgical instruments that need to be manufactured to the highest standard so that they can be relied upon to deliver their intended purpose. This is what the chemical etching achieves – precision and reliance on an industrial scale.
Part of its appeal is that the chemical process leaves the metal exactly as you want it: the finished components are burr and stress free which means that production time is shorter as there’s no need to deburr and as a result this is reflected in the cost. It’s also great for prototyping as the process is not only quick in itself but also upscaling the process to large quantity production is essentially immediate from when the prototype is finalised. So it’s clear to see why this manufacturing process is so popular across so many different industries.
The Process
Broadly speaking, chemical etching is a subtractive manufacturing process that uses temperature-regulated chemicals to selectively remove parts of a metal. At Tecan, we follow a 6-step process as follows:
1 – Cleaning
The sheet metal is cleaned of all surface contaminants to ensure the success and accuracy of the manufacturing processes.
2 – Laminating
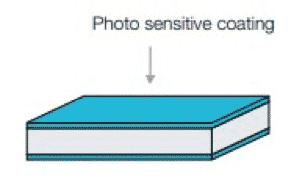
In a class 6 clean environment, a light-sensitive photoresist is applied to the metal which will later protect the wanted parts while the unwanted get removed.
3 – Exposing
The metal sheet is then exposed to UV light which then hardens the desired pattern of the photoresist/ the stencil. So in the above image, the white sections are hardened which leaves the black areas to remain unexposed so that they can be treated with etchant.
4 – Developing
Now the unexposed parts are developed away, leaving the bare metal underneath ready to receive the chemical etchant.
5 – Etching
In this step of the process, the etchant is sprayed at high pressure on both sides of the metal which precisely removes the unwanted metal.
6 – Stripping
The resist is removed to reveal the final product: the desired shaped metal which is both burr and stress free. Of course, as an industrial production method this is done across the entire sheet of metal so the process is easily repeatable and accurate across the entire sheet.
Almost any metal can undergo the etching process but some of the most common include:
- A wide range of austenitic, martensitic and ferritic stainless steels
- mild steel, carbon steel, spring steel, tool steel
- aluminum: including aircraft/aerospace grades
- nickel alloys: inconel, mu-metal, alloy 42
- brass, phosphor bronze, beryllium copper, nickel silver
Many other materials can undergo this process but do check with the manufacturer to see what options are available.
The Key Benefits of Chemical Etching
As mentioned above, one of the main factors for choosing chemical etching is that at the end of the process, the product comes out burr and stress free which means less time spent finishing the product which is in turn reflected in the total production cost. The use of etchants also allows for the elimination of cold working which is commonly used in stamping and punching machining. Similarly, it also removes the need for heat affected zones or recast layers for laser and wired electrical discharge machining. These 2 processes, as a result of their using high energy methods to cut away at the metal, can tamper with the structure and ductility of the material which isn’t always wanted. Chemical etching leaves the metal’s properties unaffected which is another great feature of this specific manufacturing process.
As you can see there are many many great reasons to use chemical etching for your production needs. And many ways in which to implement these metal products into a wide variety of industries. It offers a great deal of precision, reliance and adaptability which is why chemical etching has made a name for itself in precision metal parts manufacturing.